What Are Packaging Machines And Equipment Used For?
Packaging equipment and machines are used for packaging products at large scales with automated processes. They can include vacuum packaging machines, filling machines, sealing machines, labeling machines, box forming machines, etc. The advantages of these systems include faster and more efficient and lower labor costs and better packaging quality. They are expensive to maintain and acquire and require technical know-how to operate properly.
These Are The Fundamental Principles Of Equipment Used For Packaging:
Protection- Packaging equipment should protect the product from damage, contamination, and deterioration during storage, transportation, and distribution.Containment- Packaging equipment should contain the product in a secure and stable manner, preventing spillage, leakage, and waste.
Convenience- Packaging equipment should allow the product to be accessible, easy to use and easy to the user.
Efficient processing- Packaging equipment is required to be designed to maximize efficiency, cut waste, accelerate production and improve product quality.
Cost-Effectiveness The packaging equipment must offer the most optimal balance of cost and performance while also providing value to the client while remaining financially feasible.
Usability- The equipment used for packaging is required to be user-friendly, maintain, and clean. This ensures that workers are safe and can do their work safely.
Sustainability- Packaging equipment should be environmentally sustainable. It should minimize the amount of material used, minimize waste and have an impact that is minimal on the environment.
These principles can ensure that packaging equipment delivers the quality, security, and convenience wanted by both the producer as well as the user. Read the top rated Space utilization for blog examples.
What Are The Vacuum Packaging Filling, Sealing Cooling, Labeling, And Box Forming Machines Work?
Vacuum packaging machines- This device removes air from a bag that contains a product and seals it with a heat sealer to preserve the shelf-life of the item. They usually use an air sealer or vacuum pumps to eliminate air from the bags , and then seal the bags. Filling machines- These machines are used to fill bags and containers with product. They can be set up to disperse a specific amount of product. They are usually utilized for the production of pastes and liquids.
Machines for sealing They can be utilized in the production of food, medical supplies, and electronic items.
Labeling machines (also known as labeling machines) These machines place labels to packages or products. They can make use of labels that are heat-sensitive, pressure-sensitive, or pressure-sensitive, or glue to attach the label onto the product.
Box forming machines- These machines form cartons or boxes from flat pieces of paperboard. They can fold and glue the paperboard to make the desired shape. They then make the box ready for packing and shipping.
In each of these devices and machines, there are many technologies used, such as controls, sensors and mechanical systems. They complete their jobs in a way that is efficient and automated using a variety of technologies. For increased efficiency and speed they can be integrated into larger manufacturing lines. Have a look at the recommended staff training for site info.
Automated scaling cooling solutions provide an efficient and automatic temperature control for various applications like food production as well as biotech and pharmaceutical manufacturing as well as other industrial processes. These solutions typically use modern technologies like temperature control systems, heat exchangers, and refrigeration units to make sure that the temperature is controlled precisely and that the product is secure and reliable. Automated and scalable cooling solutions are able to meet the particular requirements of customers. They can be easily scaled to meet changing demands for production. Additionally, they can be integrated into other manufacturing systems in order to increase efficiency, boost overall production and reduce the amount of downtime. Automated, scalable cooling solutions can improve product quality, reduce the time between failures, and improve efficiency of energy. Check out the most popular sequential monoblock solutions for site tips.
What Are The Main Factors To Look At When Purchasing Packaging Equipment
Packaging requirements- The type of packaging equipment chosen will be based on the quantity of production desired.
Integration- The integration of packaging equipment into existing production lines should be taken into consideration, including compatibility and ease of integration.
Support and Maintenance. You should evaluate whether there are support and maintenance options available, and how much it costs and how easy it is to keep the equipment in good condition.
Cost- It's crucial to include the costs for the equipment as well as all associated expenses (e.g. training and maintenance, as well as installation) in the overall budget.
Energy efficiency- Energy efficiency and its associated costs must be consideredsince energy consumption can have an enormous impact on operating costs.
It must be easy to use.
Conformance with industry standards. It is crucial to comply with relevant industry standards (e.g. food safety regulations) to ensure that equipment is appropriate for its intended use.
These factors will help you make an informed choice when buying packaging equipment. Follow the top Regulating temperature for blog recommendations.
What Do You Need To Be Aware Of Regarding Product Safety And Heat Seals?
The process of heat sealing is used to seal bags or packages made of heat-sealable material like plastic. The process uses heat and pressure in order to bond materials. This creates a durable seal that can last for years.
Packaging that is reliable seals A high-quality heat seal is vital for ensuring reliability. Inadequate sealing could cause loss of product, spoilage, or leaks.
Automated Packaging Methods- Heat sealing is often automated equipment which increases the efficiency and also the consistency of the product.
Robotics/programmable Logic Controllers- Robotics/programmable logical controllers are commonly used in automated packaging processes.
Preventive maintenance plan for packaging machinery. Regular maintenance of packaging equipment (including equipment for heat sealing) is crucial to preserve its dependability and extend its life span.
The cost-effectiveness of packaging materials Heat sealing film can make a big difference in the overall cost-efficiency of packaging. Choosing the right film can help reduce waste, increase production speeds, and increase product quality.
Price reduction for packaging It is vital to optimize the packaging process which includes heat sealing in order to reduce wasted packaging and improve efficiency.
Processes for packaging- Heat sealing is just one part of the larger packaging procedure that includes additional steps like filling, labeling and packaging. It is essential that you understand the whole process, and how heat-sealing is incorporated within it, to run a profitable and efficient packaging business. Read the most popular Baumer for website advice.
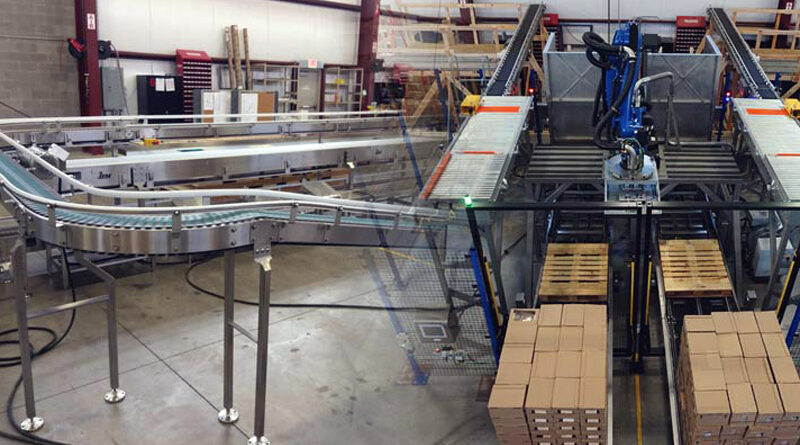 |